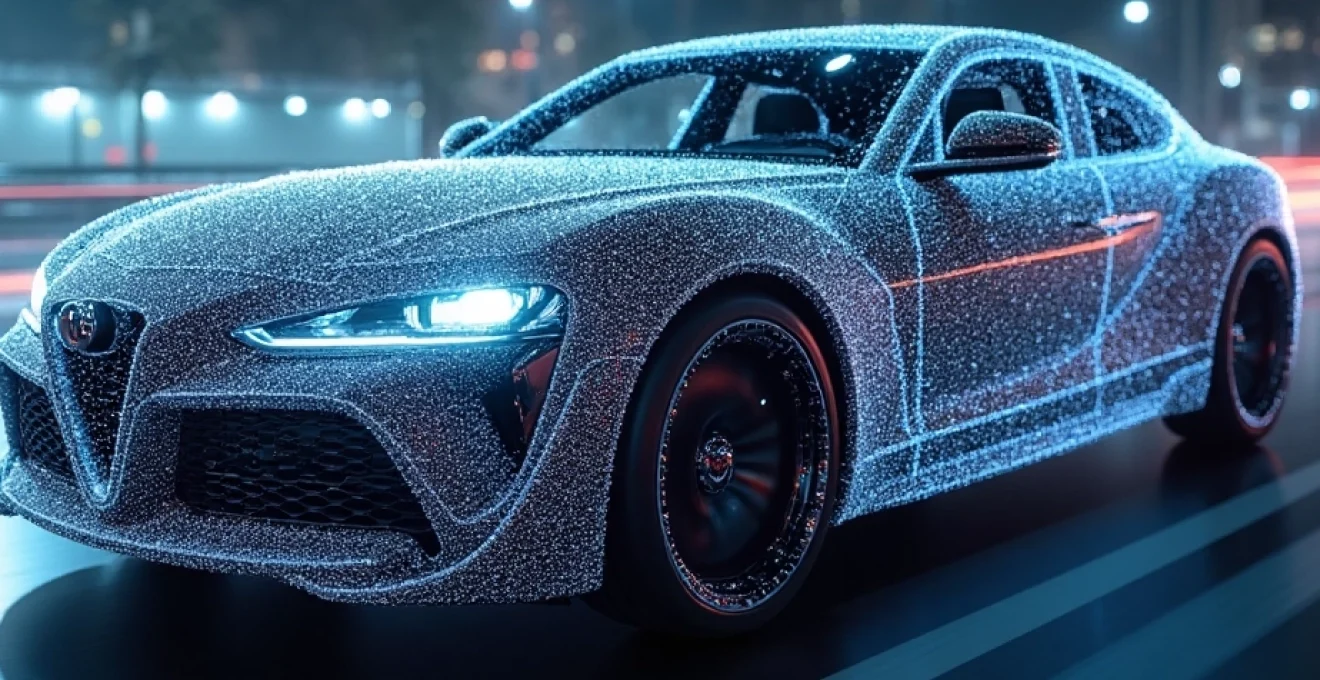
The automotive industry is undergoing a profound transformation, driven by the urgent need to reduce carbon emissions and improve fuel efficiency. Engine manufacturers are at the forefront of this revolution, developing innovative technologies that push the boundaries of what’s possible in internal combustion engines. From advanced combustion techniques to sophisticated turbocharging systems, these new engines are redefining performance while significantly lowering environmental impact.
As global regulations tighten and consumer demand for greener vehicles grows, the race to create more efficient engines has intensified. This push for innovation has led to remarkable advancements in engine design, fuel management, and emissions control systems. The result is a new generation of engines that not only meet stringent environmental standards but also deliver the power and drivability that consumers expect.
Advanced combustion technologies in modern engines
One of the most significant areas of development in modern engine design is advanced combustion technologies. These innovations aim to optimize the fuel burning process, extracting maximum energy while minimizing harmful emissions. Engineers are exploring various techniques to achieve this delicate balance, including homogeneous charge compression ignition (HCCI) and low-temperature combustion (LTC).
HCCI combines elements of both gasoline and diesel engines, using compression to ignite a homogeneous mixture of fuel and air. This process results in more complete combustion, reducing emissions and improving fuel efficiency. However, controlling HCCI combustion across a wide range of engine speeds and loads remains a challenge that researchers are actively working to overcome.
LTC, on the other hand, focuses on reducing peak combustion temperatures to minimize the formation of nitrogen oxides (NOx) and particulate matter. By carefully controlling fuel injection timing and using high levels of exhaust gas recirculation, LTC engines can achieve ultra-low emissions without sacrificing performance.
Advanced combustion technologies are paving the way for engines that can meet future emissions standards while delivering the power and efficiency that consumers demand.
Another promising technology is gasoline compression ignition (GCI), which applies diesel-like compression ignition to gasoline fuel. This approach combines the best attributes of both fuel types, offering high efficiency and low emissions. Major automakers are investing heavily in GCI research, with some prototype engines showing remarkable improvements in fuel economy compared to conventional gasoline engines.
Turbocharging and supercharging innovations
Turbocharging and supercharging have long been used to boost engine performance, but recent innovations have taken these technologies to new heights. Modern forced induction systems are not just about increasing power; they’re crucial tools in the quest for better fuel efficiency and lower emissions.
Variable geometry turbochargers (VGT) in diesel applications
Variable Geometry Turbochargers (VGT) have revolutionized diesel engine performance. By adjusting the angle of the turbine vanes, VGTs can optimize boost pressure across a wide range of engine speeds. This technology eliminates turbo lag at low speeds while preventing over-boosting at high speeds, resulting in improved throttle response and better overall efficiency.
In diesel engines, VGTs play a crucial role in emissions control by enabling precise exhaust gas recirculation (EGR) management. The ability to control boost pressure accurately allows for optimal EGR rates, which is essential for reducing NOx emissions without compromising fuel economy or performance.
Electric turbocompounding systems for energy recovery
Electric turbocompounding is an innovative approach to energy recovery in turbocharged engines. This system uses an electric generator coupled to the turbocharger shaft to capture excess exhaust energy that would otherwise be wasted. The recovered energy can be used to power vehicle electrical systems or stored in a battery for later use.
By harnessing this previously untapped energy source, electric turbocompounding can improve overall engine efficiency by 2-5%. This technology is particularly beneficial in long-haul trucks and other heavy-duty applications where fuel efficiency is paramount.
Twin-scroll turbochargers in gasoline direct injection engines
Twin-scroll turbochargers have become increasingly popular in modern gasoline direct injection (GDI) engines. This design separates the exhaust flow from pairs of cylinders, reducing interference and improving exhaust scavenging. The result is faster turbocharger response and better low-end torque, allowing for more aggressive engine downsizing without sacrificing drivability.
When combined with GDI technology, twin-scroll turbochargers enable engines to operate with higher compression ratios, further improving efficiency. This synergy between advanced turbocharging and precise fuel injection is a key factor in the impressive performance of many modern turbocharged gasoline engines.
Electrically assisted turbochargers for lag reduction
One of the most exciting developments in turbocharging technology is the electrically assisted turbocharger. By integrating an electric motor into the turbocharger assembly, these systems can provide instantaneous boost pressure, effectively eliminating turbo lag. The electric motor spins up the compressor wheel rapidly, providing boost even before the exhaust gases have enough energy to drive the turbine.
Electrically assisted turbochargers not only improve throttle response but also allow for more efficient engine operation. The ability to precisely control boost pressure enables better matching of airflow to engine load, resulting in improved fuel economy and lower emissions across a wide range of operating conditions.
Hybrid powertrain integration for enhanced efficiency
The integration of electric power with internal combustion engines has opened up new possibilities for improving efficiency and reducing emissions. Hybrid powertrains come in various configurations, each offering unique benefits depending on the application.
48V mild hybrid systems: Mercedes-Benz EQ boost technology
48V mild hybrid systems have gained significant traction in recent years, offering many of the benefits of hybridization without the complexity and cost of full hybrid powertrains. Mercedes-Benz’s EQ Boost technology is a prime example of this approach, combining a 48V electrical system with a conventional internal combustion engine.
The EQ Boost system uses an integrated starter-generator (ISG) that can provide additional power during acceleration, recover energy during braking, and enable seamless start-stop operation. This technology can improve fuel efficiency by up to 15% while also enhancing performance and drivability.
Plug-in hybrid electric vehicle (PHEV) architectures
Plug-in hybrid electric vehicles (PHEVs) represent a significant step towards full electrification, offering the ability to drive on electric power alone for short distances while retaining the long-range capability of a conventional engine. PHEV architectures vary, but most combine a high-capacity battery pack with an electric motor and a downsized internal combustion engine.
The latest PHEV systems are becoming increasingly sophisticated, with intelligent power management systems that optimize the use of electric and combustion power based on driving conditions and user preferences. Some PHEVs can even use GPS data to predict upcoming terrain and adjust power delivery accordingly, maximizing efficiency.
Toyota hybrid synergy drive: continuous evolution
Toyota’s Hybrid Synergy Drive (HSD) system has been a benchmark in hybrid technology for over two decades, and it continues to evolve. The latest iterations of HSD feature more compact and efficient electric motors, improved battery technology, and sophisticated power control units that seamlessly blend electric and combustion power.
One of the key advancements in recent HSD systems is the use of a dual motor-generator setup, which allows for more flexible power distribution and improved regenerative braking efficiency. This configuration enables the system to operate in various modes, including series hybrid, parallel hybrid, and pure electric, depending on driving conditions and battery state of charge.
Innovative fuel management systems
Advancements in fuel management technology have played a crucial role in improving engine efficiency and reducing emissions. Modern fuel systems are capable of precise control over fuel delivery, enabling optimized combustion across a wide range of operating conditions.
Direct injection technology has become ubiquitous in both gasoline and diesel engines, offering numerous benefits over traditional port injection systems. In gasoline engines, direct injection allows for higher compression ratios and more precise fuel metering, resulting in improved efficiency and power output. For diesel engines, common rail direct injection systems enable multiple injection events per cycle, reducing noise and emissions while improving combustion efficiency.
Another significant development is variable valve timing and lift (VVT&L) technology. By adjusting valve timing and lift based on engine speed and load, VVT&L systems can optimize airflow into and out of the cylinders, improving efficiency and power delivery. Some advanced systems, such as Fiat Chrysler’s MultiAir technology, use hydraulic actuation to provide infinitely variable valve lift, further enhancing engine flexibility and efficiency.
The integration of advanced fuel management systems with sophisticated engine control units has enabled unprecedented levels of optimization, pushing the boundaries of what’s possible with internal combustion engines.
Cylinder deactivation is another innovative fuel management technique that has gained popularity, especially in larger engines. By shutting down cylinders during light load conditions, this technology can significantly improve fuel efficiency without compromising performance when full power is needed. Some recent systems can even vary the number of active cylinders continuously, providing seamless transitions and optimal efficiency across all driving conditions.
Exhaust gas recirculation (EGR) and selective catalytic reduction (SCR)
Emissions control technologies have become increasingly sophisticated as regulations have tightened. Two key technologies that have emerged as critical components in modern engines are Exhaust Gas Recirculation (EGR) and Selective Catalytic Reduction (SCR).
Low-pressure EGR systems in gasoline engines
While EGR has long been used in diesel engines to reduce NOx emissions, it’s now finding applications in gasoline engines as well. Low-pressure EGR systems, which recirculate exhaust gases after they’ve passed through the catalytic converter, are particularly effective in turbocharged gasoline engines. This approach helps reduce pumping losses and improves knock resistance, allowing for more efficient operation at high loads.
The implementation of low-pressure EGR in gasoline engines has enabled manufacturers to use higher compression ratios and more aggressive turbocharging, resulting in improved fuel efficiency without sacrificing performance or emissions compliance.
Dual-loop EGR for optimized NOx reduction
Dual-loop EGR systems combine the benefits of both high-pressure and low-pressure EGR, offering greater flexibility in controlling exhaust gas recirculation. This approach allows for optimized NOx reduction across a wider range of operating conditions, particularly in diesel engines where EGR management is critical for emissions control.
By using sophisticated control algorithms, dual-loop EGR systems can balance the use of high-pressure and low-pressure recirculation based on engine load, speed, and temperature. This level of control helps maintain optimal combustion characteristics while minimizing emissions and fuel consumption.
Adblue injection systems in SCR technology
Selective Catalytic Reduction (SCR) technology, which uses AdBlue
(a urea-based solution) to convert NOx into harmless nitrogen and water, has become a standard feature in modern diesel engines. The latest AdBlue injection systems offer improved precision and control, ensuring optimal dosing under all operating conditions.
Advanced SCR systems now incorporate closed-loop control, using NOx sensors to continuously monitor emissions levels and adjust AdBlue injection accordingly. This approach ensures maximum NOx reduction efficiency while minimizing AdBlue consumption, reducing operating costs for vehicle owners.
Passive SCR systems for cold-start emissions control
Cold-start emissions remain a significant challenge, particularly for diesel engines equipped with SCR systems. To address this issue, some manufacturers have developed passive SCR technologies that can begin reducing NOx emissions even before the main catalyst reaches its operating temperature.
These passive systems typically use a zeolite-based catalyst that can store NOx at low temperatures and then release and convert it once the exhaust temperature rises. This approach helps ensure that vehicles can meet stringent emissions standards across a wide range of operating conditions, including cold starts and short trips.
Materials science advancements in engine design
The quest for lighter, stronger, and more heat-resistant materials has been a driving force in engine development. Advanced materials science has enabled engineers to push the boundaries of engine design, creating more efficient and durable powerplants.
Lightweight alloys, such as advanced aluminum and magnesium formulations, are being used extensively in modern engines to reduce weight and improve thermal management. These materials offer excellent strength-to-weight ratios and can withstand the high temperatures and pressures found in today’s high-performance engines.
Ceramic components are also finding their way into engine designs, particularly in areas exposed to extreme heat. Silicon nitride valves, for example, offer significant weight savings and improved heat resistance compared to traditional metal valves. This allows engines to operate at higher temperatures, improving efficiency without compromising reliability.
Carbon fiber reinforced plastics (CFRP) are being explored for use in engine components such as connecting rods and cylinder liners. While still in the experimental stage for many applications, CFRP offers the potential for significant weight reduction and improved durability in high-stress engine components.
Another area of materials science that’s making an impact on engine design is thermal barrier coatings. These advanced coatings can be applied to components like pistons and exhaust manifolds to reduce heat transfer, improving thermal efficiency and allowing for higher operating temperatures.
As engine manufacturers continue to push the limits of performance and efficiency, the role of advanced materials in engine design will only grow more critical. The ability to create components that are lighter, stronger, and more heat-resistant will be key to meeting future emissions and fuel economy standards while delivering the performance that consumers expect.